Our Services
Grounding Design and
Lightning Strike Evaluation
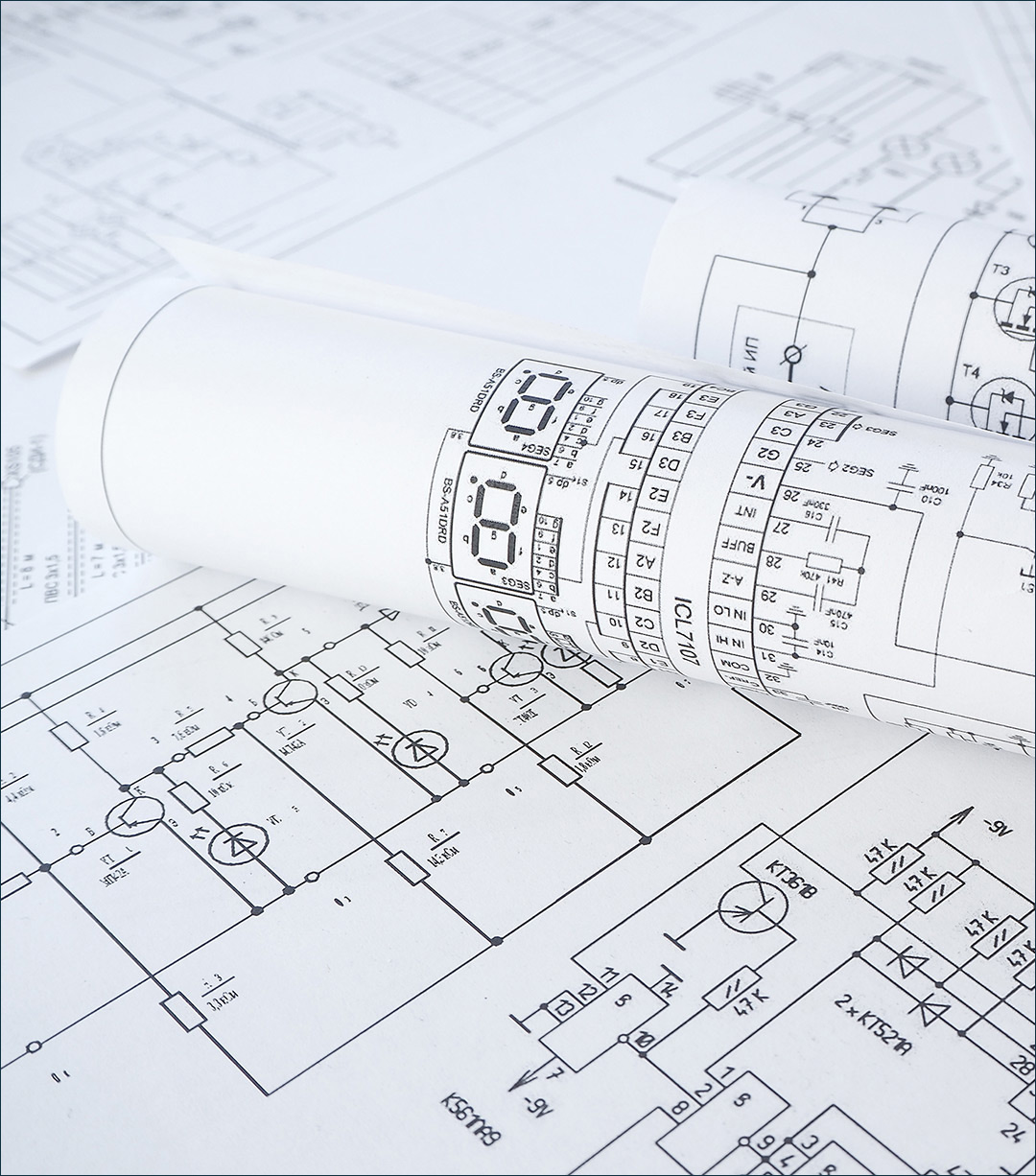
Comprehensive grounding system design improves reliability, while reducing maintenance costs, and negating downtime!
The requirements for ground resistance levels are becoming more stringent these days because of the lower operating voltages and higher operating speeds in today’s electronics. For example, telecommunications companies typically require an earth resistance of less than 5 ohms, which is less than half the resistance considered high-performance a few years ago.
The engineers at E&S Grounding Solutions can help you plan and execute an electrical grounding design that will provide the best performance ground system available, within the constraints of your available area, budget, and equipment being protected.
As the experts in electrical grounding solutions, we use specialized design software to model and build an electrical grounding system design based on the soil data, design goals, and other factors. After modeling the area, we will engineer an electrical grounding system design that will meet your performance objectives.
Soil resistivity testing is critical for high performance electrical grounding system design
Accurate soil resistivity data enables precise designs and predictable results. The type of soil, moisture, electrolytic content, and temperature also affect soil resistance. Frost line depth, water table level, bedrock, and available space dictate some specifics of the grounding system design. We determine soil resistivity using the Wenner 4 Point test method, or by analyzing soil samples. See our section on Soil Resistivity Testing for more information.
When the soil resistivity of an area is so high that a low resistance ground isn’t feasible, bonding and other requirements, such as transient voltage surge suppression (TVSS) equipment can be implemented to achieve good performance.
As part of our electrical grounding system design, the engineers at E&S Grounding Solutions provide a written recommendation along with a drawing of the site illustrating the recommended grounding configuration, quantity and location of the electrical grounding electrodes, grounding electrode spacing, and models.
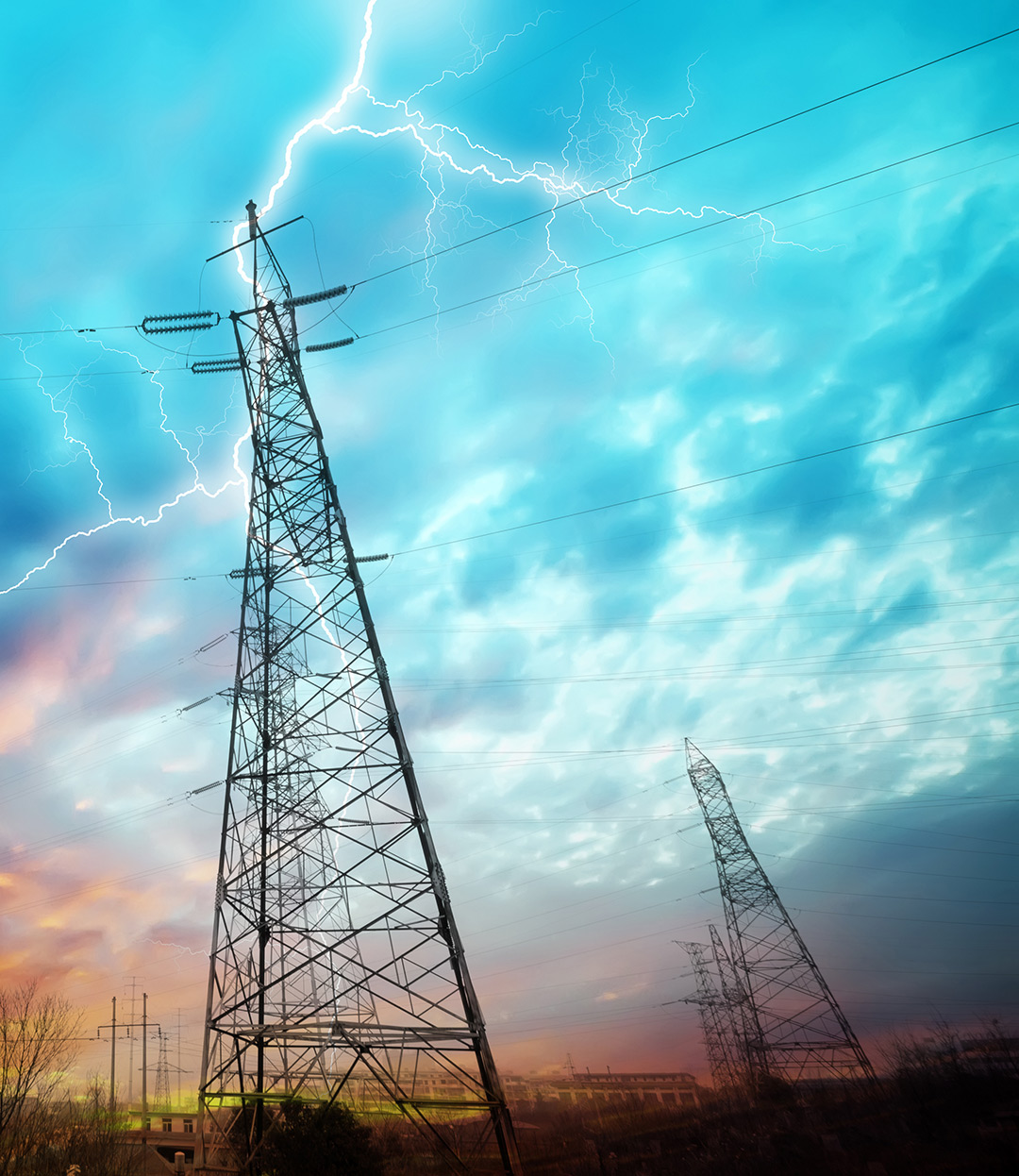
Human safety is critical during ground potential rise events in work place areas
Electrical grounding safety systems are required to protect personnel working where ground rise potential hazards are known to exist. In fact, federal law mandates that all known hazards must be eliminated from the work place for the safety of workers. Substations are always considered workplaces and step and touch potentials must be eliminated to ensure the safety of work personnel. And, although transmission and distribution towers or poles are not always considered work places and are often exempt from these requirements, as soon as equipment is installed that is not related to the electric utility company and requires outside vendors to support the new equipment, it is now considered a workplace.
Cellular telecommunications, environmental monitoring, and microwave relay equipment are good examples of equipment that, when installed on a high-voltage tower, turns the tower into a work place. Federal law 29 CFR 1910.269 specifically states that step and touch potentials must be eliminated on transmission and distribution lines that include any related communication equipment. This would make the elimination of step and touch potentials required. See our section on step and touch potential for more information.
A lightning strike analysis can save lives and sensitive equipment from injury and damage
Lightning is a random and unpredictable event. Globally, some 2000 ongoing thunderstorms cause about 100 lightning strikes to the earth each second. Did you know that total equipment damage costs from lightning strikes is aproximately 150 million dollars every year in the United States? The average lightning strike will cost approximately $30,000 in equipment damage. However, if the building and equipment is properly grounded personnel injury and equipment damage can be reduced or eliminated entirely. In fact, a Lightning Strike Analysis is a critical component in comprehensive cell site grounding design.
The purpose of a lightning protection system for a building is to provide a path for the lightning strike to pass through without damaging personnel or sensitive equipment in the building. A lightning protection system provides a low-resistance path for the strike to flow through.
The main components of a lightning protection system are:
• Grounding rods
• Air terminals
• Down conductors
The option to install a lightning protection system is a critical decision for the purposes of safety of personnel, protection of property, insurance costs, and downtime. The engineers at E&S Grounding Solutions provide lightning stike analysis based on the requirements set out in the 2000 edition of NFPA 780 Risk Analysis Guidelines (National Fire Protection Association Standard for the Installation of Lightning Protection Systems).
Let's Talk! Schedule a Free Phone Consultation Today.
Schedule a FREE Discovery Call with David Stockin, Founder CEO and Managing Partner.
Wherever you are located, let's meet in a 15-minute call and see how we can assist with your project.
Do you prefer to reach us via email?
Ask the Grounding Experts.